Torque Measurement Explained: Tools, Techniques, and Tips
When it comes to precision, safety, and reliability in mechanical work, one term stands out: torque measurement. Whether you’re tightening lug nuts on a car, assembling industrial machinery, or fine-tuning a bike, understanding how torque works and how to measure it accurately is essential. Torque measurement ensures that fasteners are tightened to the exact specification, preventing under-tightening, which could lead to equipment failure, or over-tightening, which risks damaging components.
But how is torque measured, and why does it matter? In this guide, we’ll break down everything you need to know, from the tools used to the units of measurement and practical applications for
Torque Measurement: What It Is and Why It Matters
Torque, in its simplest terms, is the rotational force applied to an object. Think of using a wrench to tighten a bolt—the force you apply to the wrench handle creates torque, ensuring the bolt stays securely in place. Torque measurement is the process of quantifying that force to ensure it meets the specific requirements for a given application.
Real-World Importance
Accurate torque measurement isn’t just a nice-to-have—it’s a must in many industries:
- Automotive: Properly torqued lug nuts ensure wheels stay secure under high speeds and stress.
- Bicycles: Precision is key to avoid damaging lightweight components like carbon fiber frames.
- Industrial Machinery: Incorrect torque can lead to catastrophic equipment failures, downtime, and costly repairs.
- Aviation: From 2009 to 2015, the National Transportation Safety Board identified over 45 aviation incidents caused by improper torque application during maintenance, leading to internal engine damage and failures (NTSB).
Risks of Improper Torque Measurement
Failing to measure and apply the correct torque can result in:
- Under-tightening: Fasteners may loosen over time, leading to equipment failure or safety hazards. In fact, insufficient torque can lead to loose connections, especially under vibrational loads, causing dangerous detachments of components or entire assemblies (TechMeStuff).
- Over-tightening: Excess force can damage threads, deform components, or compromise the material integrity.
By ensuring accurate torque measurement, you can guarantee optimal performance and longevity for your tools and machinery.
Understanding Torque Units
Torque is typically measured in three main units, and knowing how to work with them is crucial for consistency and accuracy across applications.
Common Torque Units
- Newton-meters (Nm): Used predominantly in Europe and other metric system countries. Commonly seen in automotive and industrial specifications.
- Foot-pounds (ft-lb): Widely used in the United States, especially for automotive and heavy machinery applications.
- Inch-pounds (in-lb): Ideal for smaller, more precise tasks, such as electronics or bicycles.
Torque Conversion Basics
Understanding conversions between these units is helpful when working with diverse tools and specifications:
- 1 ft-lb = 1.35582 Nm
- 1 in-lb = 0.113 Nm
- 1 Nm = 8.85075 in-lb
Using conversion tools or tables can simplify the process, ensuring you’re applying the correct torque regardless of the specified unit.
Applications of Each Torque Unit
- Nm: Most commonly specified in bicycles and European vehicles.
- ft-lb: Standard for larger automotive applications, such as lug nuts or suspension systems.
- in-lb: Ideal for precision work, like securing small bolts on electronic or bike components.
How Is Torque Measured?
Measuring torque accurately is a methodical process that combines the right tools with a clear understanding of specifications. Here’s a step-by-step guide to ensure precision every time:
Step 1: Select the Right Tool for the Job
The choice of tool directly impacts the accuracy of your torque measurement. We’ll discuss how to select the best tool for the task at hand in the sections to follow.
Step 2: Understand the Specified Torque Value
Refer to the manufacturer’s specifications for the recommended torque value. This is usually provided in units such as Nm, ft-lb, or in-lb. Ensure your wrench matches the specified unit to eliminate the risk of conversion errors.
Step 3: Apply Torque Using the Tool
Once equipped with the right wrench:
Recheck if Necessary: Double-check the torque on critical fasteners to ensure accuracy.
Attach the wrench securely to the fastener. Ensure the tool is aligned correctly to avoid uneven force application.
Turn the Wrench: Apply steady, even pressure until the desired torque is reached. For click wrenches, listen for the distinct “click.” With digital models, monitor the display closely.
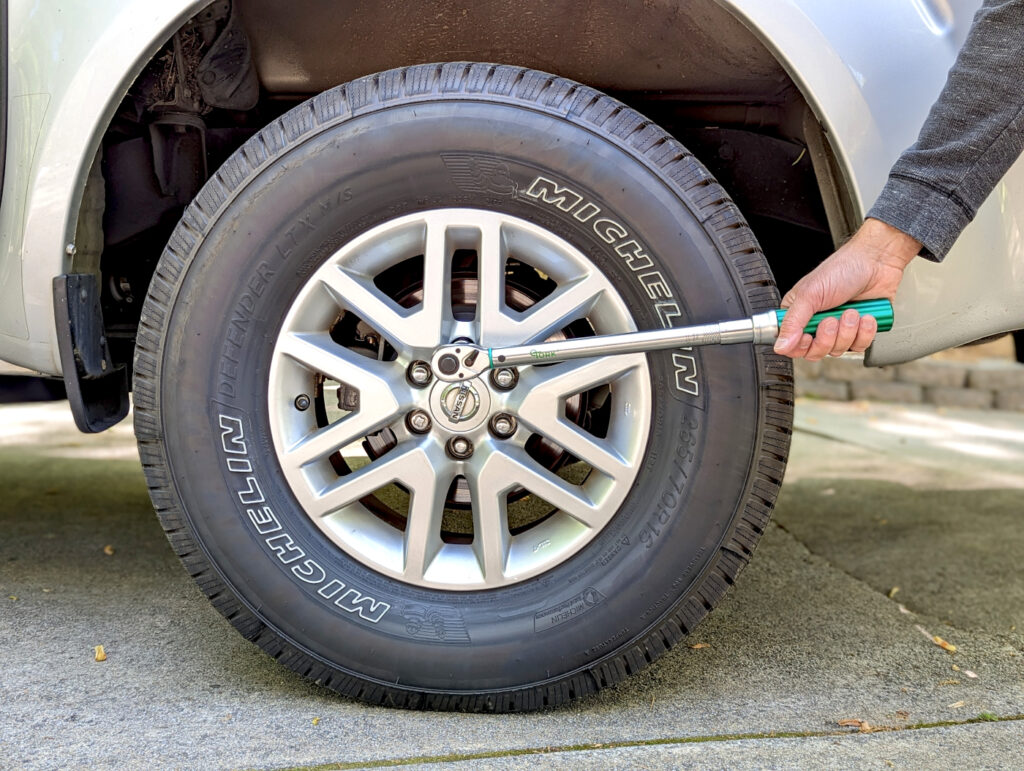
Tips for How to Measure Torque Accurately
Achieving precise torque measurement goes beyond just owning the right tools—it’s about how you use them. These tips will help you avoid common pitfalls and ensure consistent results:
- Use the Correct Wrench Size and Type: Matching the wrench to the job is critical. A digital torque wrench is best for precision tasks where even slight variances matter, such as in aerospace or high-performance bikes. A click wrench works well for general automotive needs like tightening lug nuts.
- Avoid Over-Tightening or Under-Tightening: Apply force steadily and stop immediately when the desired torque is reached. Over-tightening can strip threads, while under-tightening may lead to loose connections. Practice consistent technique to develop a feel for accurate application.
- Store Tools Properly: Proper storage can extend the life and accuracy of your tools. Avoid dropping your wrenches or storing them in extreme temperatures, as these factors can affect calibration.
- Regular Calibration of Tools: Even the best torque wrenches can lose accuracy over time due to wear and tear. Regular calibrations ensure they continue to deliver reliable measurements. Invest in calibration equipment or professional torque wrench calibration services to maintain your tools’ accuracy. Many professionals recommend annual calibrations or after every 5,000 uses.
By following these strategies and leveraging high-quality tools, you’ll ensure that every bolt, nut, and fastener is secured with confidence and precision.
Choosing the Right Torque Measuring Tool
Finding the perfect torque measuring tool depends on your specific needs, whether you’re a professional mechanic or a DIY enthusiast. Here’s what to consider:
Types of Torque Measuring Tools
- Click Wrenches: Provide a simple and effective way to achieve accurate torque settings. These are ideal for general automotive work and are user-friendly for beginners.
- Digital Torque Wrenches: Offer real-time readings and data storage capabilities, making them perfect for applications requiring extreme precision, such as aerospace or high-performance vehicles.
- Beam Wrenches: A budget-friendly option for smaller jobs. While less precise, they’re durable and reliable for basic tasks.
- Dial Torque Wrenches: Provide a clear visual indication of torque applied. These are often used in calibration labs for their accuracy.
Check out our detailed guide to torque wrench types for more information.
Tips for Choosing the Right Tool
- Consider the Task: Match the wrench’s capabilities with your project’s requirements. For instance, use a click wrench for automotive tasks and a digital wrench for high-precision work.
- Torque Range: Ensure the tool’s range aligns with the specifications of your project.
- Durability: Opt for wrenches made from high-quality materials to withstand frequent use.
- Ease of Use: Look for user-friendly features like ergonomic handles, clear displays, and easy adjustment settings.
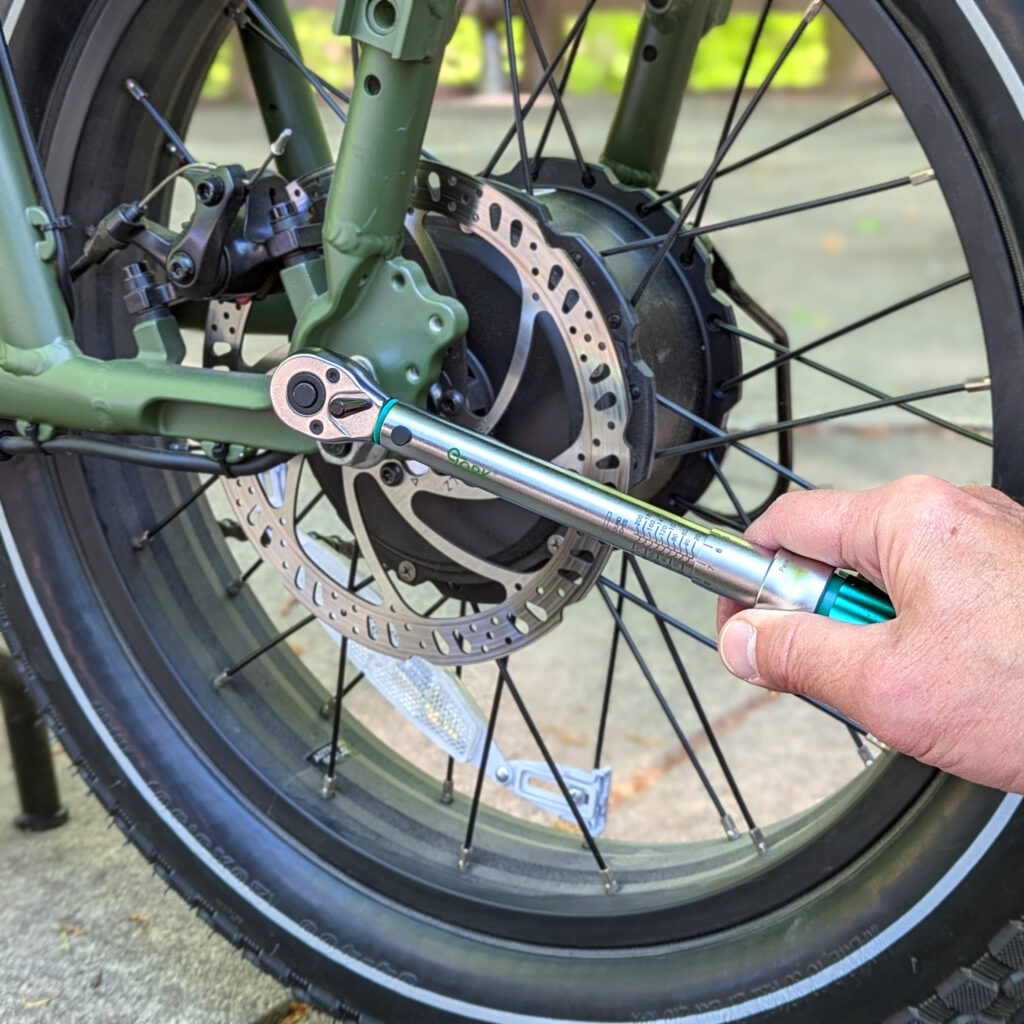
Find the Right Torque Measurement Tool with eTORK
At eTORK, we specialize in delivering precision-engineered torque wrenches that professionals and DIYers can rely on. Our tools combine advanced features with durable construction to ensure accurate and consistent results.
Why Choose eTORK Torque Wrenches?
- Precision Engineering: Our wrenches are designed to provide exceptional accuracy, ensuring your fasteners meet exact specifications.
- Durable Materials: Built to withstand tough environments, our tools are crafted from high-quality components for long-lasting performance.
- Calibration Standards: Every eTORK wrench is calibrated to meet or exceed industry standards, so you can trust your measurements every time.
Simplify Your Projects
With the right tools, torque measurement doesn’t have to be complicated. eTORK’s range of torque wrenches makes it easy to achieve professional-grade results, whether you’re working in your garage or on an industrial project.Ready to upgrade your tools? Discover our range of precision-engineered torque wrenches today!
Torque Measurement FAQs
What is torque measurement?
Torque measurement is the process of quantifying the rotational force applied to a fastener, such as a bolt or nut, to ensure it meets specific torque requirements.
How do I measure torque at home?
Use a calibrated torque wrench suited to your task. Follow the manufacturer’s instructions, and ensure you apply steady, even force until the desired torque is achieved.
Which torque measuring tool is best for beginners?
Click torque wrenches are an excellent choice for beginners due to their simplicity and reliability. They provide a clear “click” signal when the desired torque is reached.
How often should I calibrate my torque wrench?
Calibrate your torque wrench annually or after 5,000 uses, whichever comes first. Frequent users or those in critical industries may need to calibrate more often.
What are the most common torque units used in automotive work?
In automotive applications, torque is typically measured in foot-pounds (ft-lb) or Newton meters (Nm), depending on the region.