How to Use a Torque Wrench: A Step-by-Step Guide
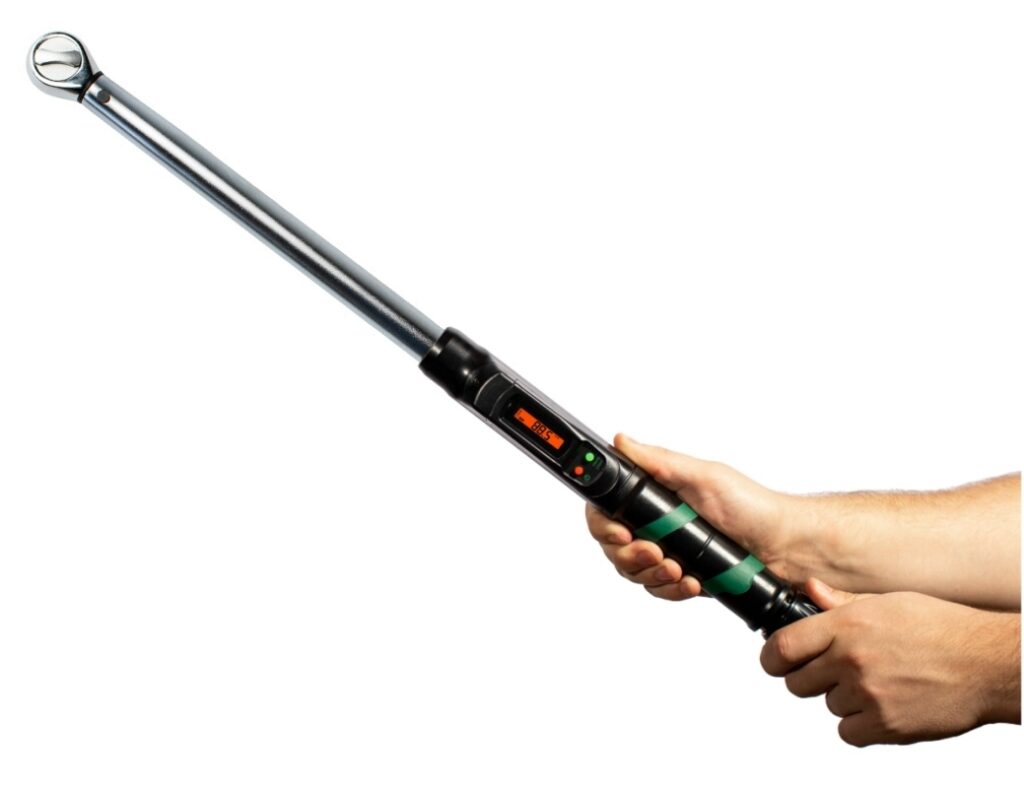
Ever wondered how to use a torque wrench properly? Well, wonder no more. We will unravel the mysteries of this handy tool so that you can wield it like a pro.
Proper torque application is crucial for safety and precision in many mechanical tasks. Incorrect torque on components like lug nuts can have serious consequences. For example, as explained by Car and Driver, over-tightening on a car wheel can warp brake rotors, reduce braking effectiveness, accelerate brake wear, and even snap wheel studs, making lugs difficult to remove. Under-tightening is equally hazardous as it may lead to lug nuts loosening or falling off, potentially causing the wheel to detach during driving. This is why vehicle owner’s manuals specify torque settings for lug nuts, emphasizing the importance of using a torque wrench correctly.
How to Use a Torque Wrench: An Overview
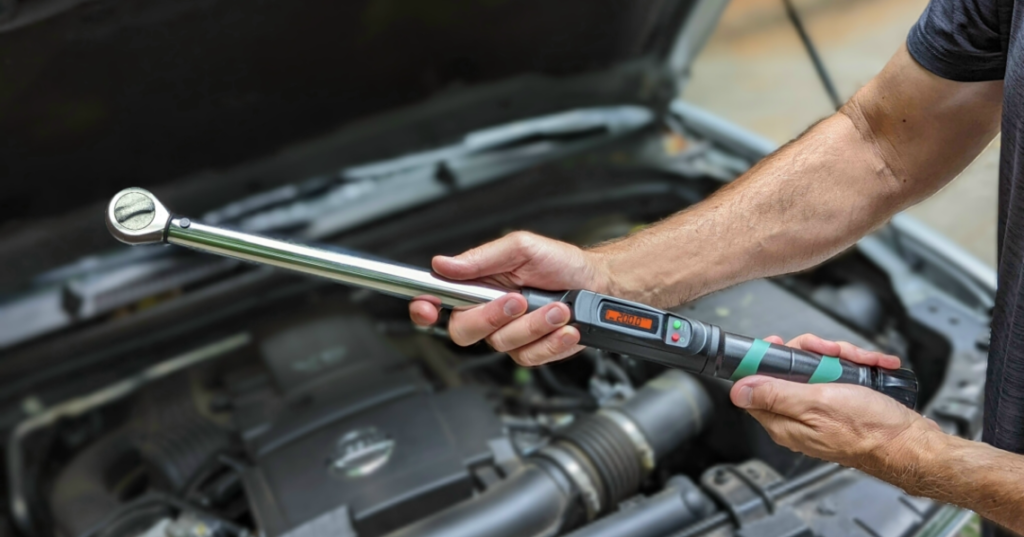
A torque wrench is not just another tool in your toolbox. It is a precision instrument designed to apply a specific amount of force to a nut or bolt. Whether working on a small appliance, a vehicle, or heavy machinery, the torque wrench allows you to achieve a perfect level of tightness without guesswork. This step-by-step guide will provide everything you need to know about using a torque wrench effectively.
What is a Torque Wrench?
First things first, what is a torque wrench? In the simplest terms, it’s a tool designed to apply a specific amount of force to a fastener, like a nut or a bolt. This precise control allows for secure and safe tightening of fastenings without causing damage.
How to Choose a Torque Wrench
So, how does one go about using a torque wrench? Well, it’s not rocket science. The first step is to choose the right wrench for the job.
If you’re ready to shop for a torque wrench, you need to understand the different types available, as torque wrenches come in different sizes, each designed for a specific range of force. A smaller wrench, like an inch-pound wrench, is ideal for delicate tasks, while a larger foot-pound wrench is more suited for heavy-duty jobs. Currently, eTORK offers three different types of wrenches, all with ranges to cover whatever torque requirement you may need. We offer Digital Scale Torque Wrenches, Analog Torque Wrenches, and our “patent pending” Micrometer Torque Wrenches.
To select the right wrench, consider the job at hand. For automotive work, a foot-pound wrench is typically necessary, but for electronics or appliance repair, an inch-pound wrench might be more appropriate.
How to Read a Torque Wrench
Reading a torque wrench is an essential skill that requires understanding the tool’s scale. Digital torque wrenches display the torque value clearly, but for analog wrenches, you need to read the scale on the handle. Here’s how to read the three primary types of torque wrenches:
Digital Scale Torque Wrenches:
- Power On and Set Torque: Activate the wrench and set the desired torque value using the digital interface.
- Monitor the Display: As you tighten the fastener, the digital screen on the wrench will display the desired torque value. eTORK wrenches are click-style; listen for a clear click which indicates that the desired torque has been reached. This sound confirms accurate and reliable tightening.
Analog Torque Wrenches:
- Read the Dial: These wrenches are equipped with a dial that displays the desired torque value. Observe the needle’s position on the dial to set the torque accordingly.
- Check for Desired Torque: eTORK’s wrenches are designed as “click-style” models. Simply tighten the fastener and listen for the click, which indicates that you have reached the set torque value. This audible signal ensures consistent and precise application.
Micrometer Torque Wrenches:
- Adjust to Desired Torque: Set the torque by turning the micrometer adjuster until the scale aligns with your desired setting.
- Listen for Click: Tighten the fastener until you hear a click sound or see the head release, indicating that the preset torque has been reached. Avoid any further tightening to prevent overtightening.
Each type of torque wrench has a unique method for displaying your desired torque setting, so familiarize yourself with the specific features of your tool. Remember to always ensure that you’re reading the torque values in the correct unit of measure as per your task requirements. Proper reading is essential for achieving precise fastening without the risk of damage.
How to Set a Torque Wrench
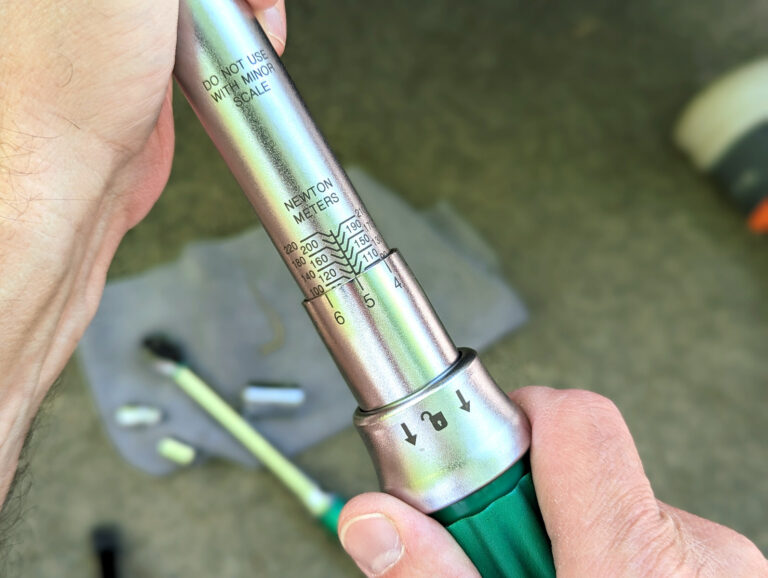
Once you’ve selected your wrench, the next step is to set the desired torque. This is usually indicated in the manufacturer’s instructions or on the fastener itself. To set the torque, rotate the handle until the correct measurement aligns with the mark on the wrench’s shaft. Make sure to double-check this setting; accuracy is key.
For a more detailed guide, follow these steps:
- Identify the Torque Requirement: Refer to the manufacturer’s instructions or project specifications to find the required torque value for the fastener you are working with.
- Locate the Adjustment Mechanism: Find the handle or dial on your torque wrench that is used for setting the torque. This is typically at the end of the handle.
- Adjust the Torque Setting: Turn the adjustment mechanism to align with the desired torque value on the wrench’s scale. Some wrenches may have a locking mechanism to ensure the setting does not change during use.
- Lock the Setting: If your wrench has a locking mechanism, secure it once the correct setting is achieved. This prevents any accidental changes while you are working.
- Double-Check the Setting: Before you start tightening, verify the torque setting again to ensure it’s accurate. Adjust if necessary.
These steps will help ensure that you set your torque wrench correctly, leading to optimal performance and safety in your tasks.
How to Apply Torque
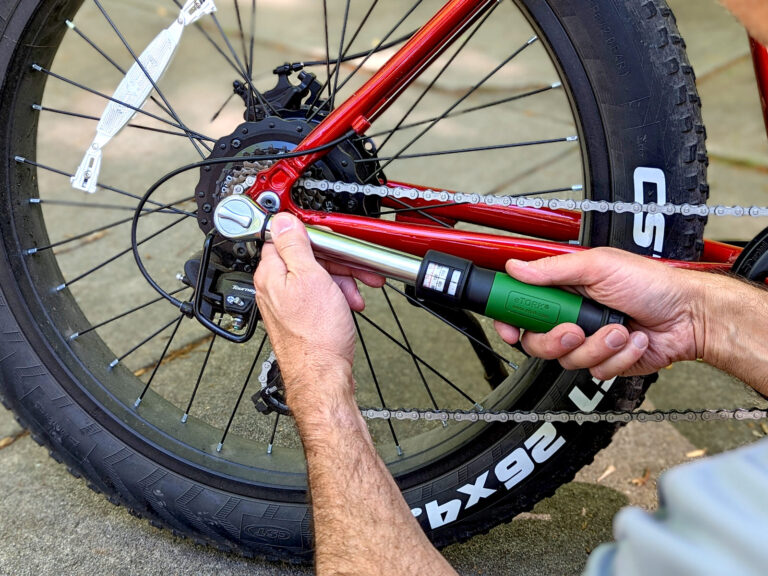
Now comes the fun part: applying the torque. Hold the wrench with both hands, placing one hand on the handle and the other near the head of the wrench. Position the wrench so that it’s perpendicular to the fastener. Start tightening the fastener in a smooth, steady motion. As you tighten, pay attention to the wrench. When the desired torque is reached, most torque wrenches will emit a click or a break in tension. This is your cue to stop. Don’t be tempted to give it an extra nudge. Over-tightening can lead to damage.
How to Reset a Torque Wrench
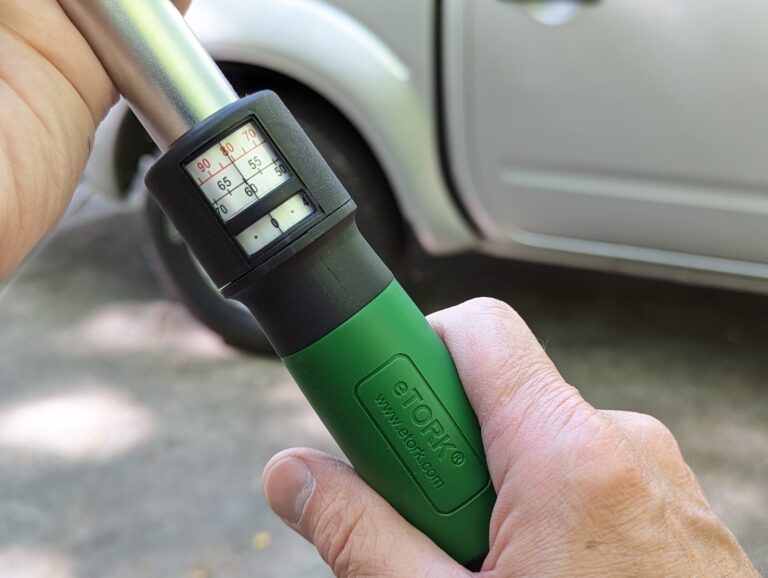
Finally, once you’ve finished your task, always remember to reset the torque wrench to its lowest setting before storing it. This helps to maintain the calibration of the wrench, ensuring it continues to provide accurate readings.
How to Adjust Torque Wrench
Adjusting a torque wrench may be necessary to accommodate different sizes of fasteners or to recalibrate the tool for accuracy after prolonged use. Generally speaking, torque wrenches should be tested for recalibration at least every 6-12 months or every 2,500-5,000 cycles, depending on use. While minor adjustments might be manageable at home, here are several reasons why it’s advisable to use a professional calibration service:
- Precision and Accuracy: Professional calibration services are equipped with the proper tools and expertise to adjust torque wrenches with high precision. This ensures that your wrench meets the manufacturer’s specifications and industry standards, which is crucial for tasks requiring exact torque values.
- Maintaining Tool Integrity: Improper handling during self-calibration can damage the internal mechanism of a torque wrench, affecting its functionality and longevity. Professionals ensure that the calibration process does not compromise the tool’s integrity.
- Certification and Compliance: For many professional settings, having a calibrated tool that comes with a certification is necessary to meet industry regulations. Professional services provide documentation certifying that the tool has been calibrated to standard specifications.
- Cost-Effectiveness: While recalibrating a torque wrench yourself might seem like a cost-saving measure, incorrect adjustments can lead to costly errors due to improperly torqued fasteners. Using professional services reduces the risk of expensive rework or damage.
- Warranty Preservation: Many torque wrench manufacturers require professional recalibration to maintain the warranty on the tool. DIY recalibration might void this warranty.
eTORK wrenches come with a free calibration service warranty, which you can learn more about at eTORK Calibration Services.
Conclusion: A Summary of How to Use a Torque Wrench
To summarize, using a torque wrench involves these key steps: choosing the right wrench, understanding how to read the wrench, setting the desired torque, applying the torque until the wrench signals you to stop, resetting the wrench before storage, and recalibrating the wrench as needed after extended use.
Remember, the beauty of a torque wrench lies in its precision. It’s not about brute force, but rather the application of the right amount of force. So, the next time you have a task that calls for a torque wrench, approach it with the confidence and knowledge that you now possess. With the right tools and a little know-how, you can tackle any task. So go forth, and tighten with confidence. The world of torque wrenches is now at your disposal. For any additional questions, reach out to us by mail or phone, we are always happy to help.