In the world of mechanical work, the precision of your tools determines the quality of your results. This is especially true for torque wrenches—a critical tool in both professional and home mechanics’ arsenals. These specialized tools guarantee that fasteners are tightened to the exact specifications, preventing anything from stripped threads to leaky connections or even catastrophic component failures. But like any precision tool, torque wrenches need regular maintenance to ensure their accuracy. This is where torque wrench calibration comes in.
Proper torque wrench calibration is not just about maintaining accuracy; it’s a safety issue that must be taken seriously. Using an uncalibrated torque wrench can lead to mechanical failures, potentially causing serious accidents. Understanding the importance of torque wrench calibration can save time and money, but most importantly, prevent life-threatening mechanical failures.
Torque Wrench Calibration 101: Ensuring Tool Accuracy and Longevity
Put simply, torque wrench calibration is the process of verifying and adjusting the tool’s accuracy. Factors such as mechanical wear, temperature changes, and accidental drops can affect a torque wrench’s performance. Regular calibration ensures that a torque wrench provides accurate readings, thereby extending its lifespan and ensuring safety during its use. eTORK offers a variety of click-type torque wrenches, known for their reliability and supported by comprehensive torque wrench calibration services.
Click Type Torque Wrench Calibration: What You Need to Know
Click-type torque wrenches, like those offered by eTORK, are renowned for their ease of calibration, making them a preferred choice in both professional and home settings. These wrenches typically feature a simple calibration process that can be quickly learned and implemented, ensuring that tools maintain high accuracy with minimal effort. These wrenches offer a distinct ‘click’ sound when the preset torque value is reached, signaling to the user that the desired torque has been applied.
The straightforward mechanism of click-type wrenches not only facilitates rapid adjustments but also enhances reliability and extends the tool’s lifespan, thereby delivering great value and performance consistency. This ease of calibration is a significant benefit, particularly for applications requiring frequent tool accuracy verification. However, as with all torque wrenches, it’s crucial to regularly check these tools for accuracy because over time and with regular use, the calibration can drift.
How to Calibrate a Torque Wrench: A Step-by-Step Guide
Calibrating a torque wrench is crucial to ensure it delivers accurate readings and maintains its reliability, which is essential for both safety and mechanical precision. Before proceeding with the step-by-step calibration guide, it’s crucial to emphasize the importance of adhering to the manufacturer’s specific instructions for calibrating torque wrenches. The steps below offer general guidance; however, consulting your wrench’s user manual for detailed procedures and specifications is essential to ensure accuracy and prevent damage.
- Initial Preparation:
- Clean the Wrench: Before starting the calibration process, make sure the wrench is clean. Remove any dirt, grease, or debris that could affect its performance.
- Reset to Zero: Adjust the torque wrench to its lowest setting or zero. This minimizes tension in the internal mechanisms, providing a neutral starting point for calibration.
- Inspection for Wear and Damage:
- Examine the Tool: Check the entire length of the torque wrench, including the handle and head, for any signs of wear or damage. Pay particular attention to the ratchet head and the torque adjustment mechanism.
- Check for Calibration Stickers: Look for the last calibration date. If it’s past the recommended calibration interval, proceed with recalibration. The absence of a sticker or an outdated sticker underscores the need for immediate calibration.
- Selecting the Proper Calibration Equipment:
- Choose an Appropriate Calibration Tool: Depending on the type and model of the torque wrench, select either a mechanical loader with a calibrated beam or a digital loader. For many click-type torque wrenches, a certified and traceable torque tester is recommended.
- Setting Up the Calibration Tool: Ensure the calibration tool is correctly set up and calibrated. Follow the manufacturer’s guidelines for setup to ensure accuracy.
- Attaching the Torque Wrench to the Calibration Tool:
- Secure Attachment: Attach the square drive of the torque wrench to the calibration tool. Make sure the connection is secure and the wrench is properly aligned with the calibration equipment.
- Load Application: Begin applying the load to the torque wrench slowly. It’s important to increase the torque gradually until you reach the desired test value.
- Reading and Adjusting:
- Monitor the Calibration Tool’s Display: As you apply the torque, keep an eye on the readings from the calibration tool. Compare these readings to the torque settings on your wrench.
- Make Adjustments: If the readings on the tool deviate from your wrench’s settings, adjust the wrench according to its adjustment mechanism. This might involve turning a screw or dial on the wrench to align the internal mechanism’s accuracy with the calibration tool’s readings.
- Verification:
- Repeat Measurements: After making adjustments, repeat the measurement process to verify that the wrench now reads accurately across its entire operating range.
- Test at Several Points: It’s advisable to test the wrench at 20%, 50%, and 100% of its maximum capacity to ensure accuracy across the range.
- Documentation and Reassembly:
- Record the Calibration: Document the calibration results, including the date, technician name, and any adjustments made. Attach a new calibration sticker to the wrench.
- Reassemble and Store: If any parts were removed or loosened during the calibration, securely reassemble them. Store the torque wrench in a controlled environment that minimizes exposure to dust, humidity, and extreme temperatures.
- Final Testing:
- Perform a Functional Test: Before declaring the calibration complete, perform a functional test by tightening a test bolt or nut to ensure the wrench clicks at the set torque value accurately.
By following these detailed steps, you can ensure your torque wrench maintains optimal performance and accuracy, safeguarding your mechanical work against potential inaccuracies and enhancing tool longevity.
Choosing the Right Torque Wrench Calibration Tool
Selecting the right calibration tool for your eTORK torque wrench involves matching the tool’s capabilities with the wrench’s specifications. For wrenches with clear-view analog scales or micrometer scales, a mechanical loader calibrated for both English and metric units ensures precision. Digital wrenches, which display multiple units such as Nm and ft-lb, may require digital calibration tools that offer a range of measurements and high accuracy.
Ensure that the calibration tool not only matches the torque wrench’s type and measurement range but also offers ease of use and reliability. This compatibility is crucial for maintaining the precision of your torque measurements and extending the lifespan of your tools, particularly for those used frequently in professional settings.
Mistakes to Avoid When Calibrating Torque Wrenches
When calibrating your torque wrench, certain common mistakes can compromise the accuracy and performance of the tool. Here’s what to avoid:
- Using Incorrect Tools: Ensure the calibration tool matches the specifications of your torque wrench. Incorrect tools can lead to poor calibration.
- Skipping Regular Checks: Regular calibration is essential. Neglecting this can cause the wrench to drift from its accurate settings.
- Ignoring Manufacturer’s Specifications: Always follow the guidelines provided by the manufacturer for calibration procedures and intervals.
DIY Calibration vs. Professional Services:
- DIY Calibration: Suitable for less critical applications and for users comfortable with mechanical tools. Always ensure you have the right equipment and knowledge.
- Professional Calibration Services: Recommended for professional and high-stakes environments where precision is critical. Professional services guarantee the highest level of accuracy and reliability and often come with certification that may be necessary for compliance in certain industries.
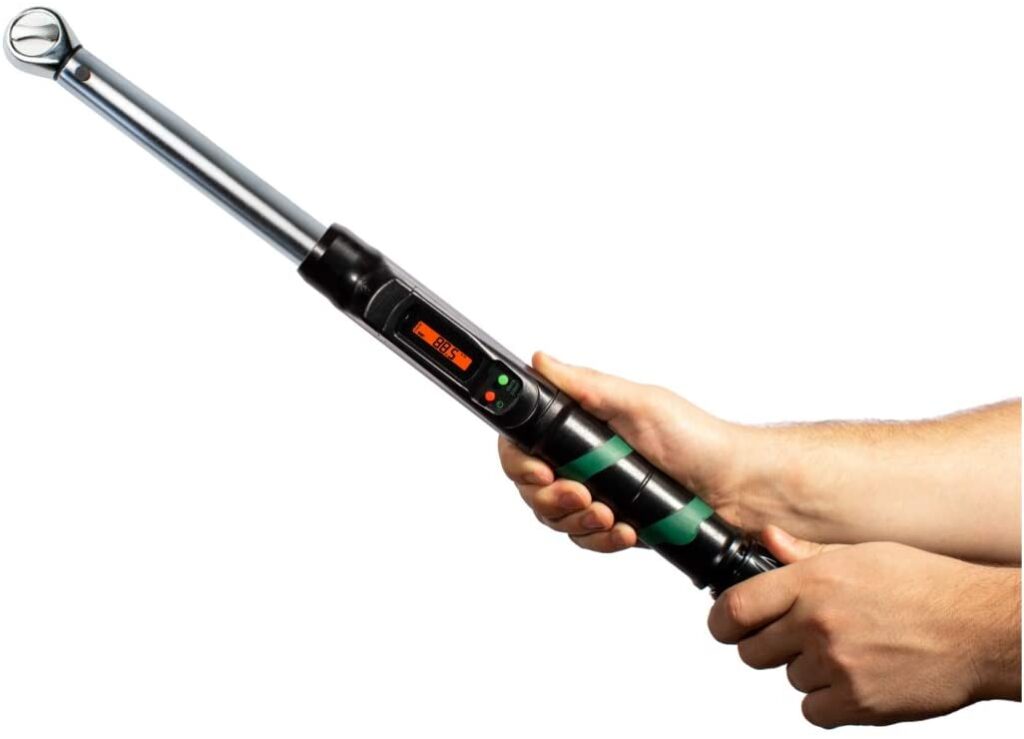
The Importance of Regular Torque Wrench Calibration Checks
Regular calibration of torque wrenches is crucial for maintaining mechanical integrity and ensuring safety. Calibration frequency should align with the tool’s usage intensity and the conditions in which it is used:
- Heavy Users: For those frequently using torque wrenches in demanding environments, calibrating every three months or after every 3,000 uses is advisable.
- Less Frequent Users: For occasional users, an annual calibration check is generally sufficient. Or immediately after it has been dropped or otherwise compromised to ensure continued accuracy (AOPA).
According to the National Institute of Standards and Technology (NIST), there is no one-size-fits-all calibration interval. Instead, NIST recommends determining calibration intervals based on several factors including the accuracy requirements of specific applications, the stability of the instrument, and environmental conditions that could affect performance (NIST). This tailored approach ensures that each torque wrench is maintained according to its specific needs and operating contexts.
Advantages of a Professional Torque Wrench Calibration Service
In general, while DIY calibration is possible, professional services ensure accuracy and reliability, especially critical in professional settings where precise torque is crucial. Professional calibration services, like those offered by eTORK, provide certified accuracy and peace of mind. All you have to do is complete a quick form and ship the tool to us— we’ll do all the required recalibration work, provide any required parts, and ship it back to you!
Maintaining Precision with eTORK Torque Wrench Calibrations
We cannot stress enough the importance of regular maintenance and calibration of your torque wrenches. Trusting a professional to handle your calibration needs ensures that your tools perform optimally and last longer. Visit our torque wrench calibration service to learn more about how we can help maintain the precision and reliability of your eTORK tools!